S2 E4 - Training Within Industry: From World War II to Modern Excellence
The Improvement Nerds Podcast - Ein Podcast von thegreendotconsultinggroup
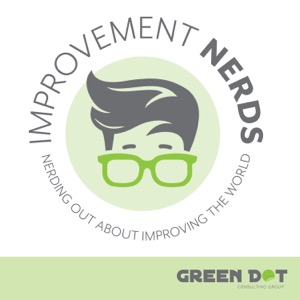
Kategorien:
S2 E4 - Training Within Industry: From World War II to Modern Excellence The Timeless Power of TWI: Building High-Performing Teams Through Training Within Industry In the world of process improvement, few methodologies have stood the test of time like Training Within Industry (TWI). Born out of necessity during World War II, TWI helped the U.S. ramp up production, train a new workforce, and ultimately achieve success in wartime manufacturing. But what makes TWI even more fascinating is its continued relevance in today’s fast-paced, technology-driven world. In our latest Improvement Nerds podcast episode, we had the privilege of diving into the world of TWI with Mark Warren, a Lean and process improvement expert with decades of experience. Mark not only unpacks the history and structure of TWI but also shows how this methodology can transform organizations by putting people at the heart of improvement. Here’s a glimpse of what we explored. What Is TWI and Why Does It Matter Today?At its core, TWI is a training methodology designed to help organizations standardize work, improve processes, and build strong relationships between employees and leaders. Originally developed during World War II, TWI equipped an untrained workforce—many of them women stepping into manufacturing for the first time—to perform highly technical tasks efficiently and safely. While TWI’s roots are in manufacturing, its principles are universal. Any organization looking to improve its operations, from healthcare to tech, can benefit from adopting TWI. The Three Pillars of TWI: JI, JM, and JRTWI consists of three main components, each addressing a specific need in the workplace: Job Instruction (JI):JI focuses on standardizing work processes and training employees effectively. By breaking down tasks into clear steps, identifying key points, and explaining the reasons behind them, JI ensures employees understand not just what to do, but why they’re doing it. This approach dramatically shortens training times and reduces quality issues. Job Methods (JM):JM is all about improving processes. It teaches leaders to evaluate workflows and identify ways to eliminate waste, reduce cycle times, and boost efficiency. Think of it as industrial engineering simplified, making it accessible to anyone tasked with process improvement. Job Relations (JR):Often overlooked, JR addresses the people side of work. It helps leaders resolve conflicts, build trust, and foster positive relationships with their teams. By focusing on clear communication and proactive problem-solving, JR creates a foundation for a healthy, high-performing workplace culture. Why TWI Still Works in the Modern WorldDespite being over 80 years old, TWI’s principles are more relevant than ever. As Mark Warren shared, TWI laid the foundation for Toyota’s production system, which is still celebrated as a gold standard in Lean manufacturing. Today, companies across industries are rediscovering TWI as a way to build leadership, improve training outcomes, and engage their workforce. One of TWI’s greatest strengths is its human-centered approach. In a world increasingly dominated by automation and AI, TWI reminds us that people remain the heart of any organization. By focusing on clear communication, effective training, and strong relationships, TWI ensures employees feel empowered and equipped to succeed. Real-World Impact: TWI in ActionMark shared compelling examples of how TWI has transformed organizations: Faster Training: Companies using JI have cut training times from weeks to days, enabling new employees to hit the ground running with confidence. Improved Retention: By providing clear instructions and meaningful training, organizations have reduced turnover and created a more engaged workforce. Enhanced Productivity: One aerospace company Mark worked with doubled productivity over five years without expanding its physical footprint, simply by integrating TWI principles into its operations. These