Machine Guarding w/ Hartley Webb
MEMIC Safety Experts - Ein Podcast von Peter Koch - Montags
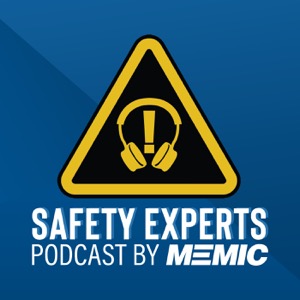
Kategorien:
Machine Guarding ranks number 9 out of OSHA’s Top 10 Most Frequently Cited Standards, with 1,743 violations in 2019. (https://ehsdailyadvisor.blr.com/2019/09/osha-reveals-latest-top-10-list-of-violations-at-nsc-2019/). According to OSHA’s Machine guarding eTool, there are over 18,000 injuries and 800 deaths each year attributed to worker exposure to unguarded or inadequately guarded machines. Does your workplace have presses, shears, gears, rollers, conveyors, or shafts? How about mixers, jointers, portable power tools, or power saws? What do they have in common? Their moving parts can cause a multitude of serious or life changing injuries like amputations, crushed limbs or digits, and blindness. And all may fall under the machine guarding standard. In this episode, Peter speaks with Hartley Webb, MEMIC’s expert on machine guarding, about what machine guarding is, hazards of unguarded machines, and common strategies to control worker exposure. Listen in as they discuss different types of guards from fixed to interlocking and self-adjusting, as well as devices like light curtains and two hand controls/trips that protect the worker from moving parts. Peter Koch: Hello, listeners. Welcome to the MEMIC Safety Experts podcast for today's episode, Machine Guarding. I'm speaking with Hartley Webb, Safety Management Consultant for MEMIC, to better understand the impact machine guarding has on us in the workplace. Hartley has been a safety management consultant with MEMIC for over 25 years, almost since its inception, working with all varieties of businesses. He's a frequent speaker for the Maine and New Hampshire Safety Councils, and Hartley is a CSP and a firefighter in his hometown in northern Maine. Hartley joins us today on the phone. And welcome to the podcast, Hartley. Hartley Webb: My pleasure. Thank you for having me. Peter Koch: Fantastic. So happy to have you here. Before we get into this topic, a little bit of talk about machine guarding. Why don't you tell me a little bit about yourself and your position here with MEMIC? Hartley Webb: Well, I graduated with industrial technology degree and I went to work for heavy industrial account work there for a few years and then was offered a job as safety consultant for heavy construction. Spent a few years in that trade. And then the insurance company that was handling the contractors working with asked me to come to work for them. And that got me into the insurance industry. And I was there for about two years when I was able to take a job with MEMIC back in 1993. And I've been with MEMIC ever since. Peter Koch: Wow. Long, long history and some good work experience to bring you in to MEMIC to be a safety consultant. And certainly so really having that heavy industry experience gives you some insight into machine guarding across the board, whether it be through heavy industry or it could be in the many woodworking shops that we have here in Maine or any of the manufacturing or industrial operations that we have across the England or throughout any of our insureds. Peter Koch: So, we're to talk a little bit about well, a lot about machine guarding today. And what I'd like to know from you is like, what is the definition? Let's start with that. What's the definition of safeguarding or machine guarding? Hartley Webb: Well, the idea behind machines safeguarding is to prevent the accidental contact with some hazard operation associated with a piece of machinery. And there's various types of hazards. We'll probably get into discussing, but the whole goal behind it is to prevent that accidental contact with those hazard areas, either while operating machines, servicing a machine or working in proximity to a machine. Peter Koch: Ok, so accidental contact, obviously, you know, no machine guarding is going to prevent a purposeful contact with a hazard operation of the machine. So accidental contact. Is it designed to have there for normal operations, or for maintenance operations? Does it have to be there all the time? So, is it designed to protect the employee at all times or are there certain times where the machine guard doesn't need to be there? Hartley Webb: The machine safeguarding should be there at all times. Anytime that safeguard is either removed or bypassed, that would bring about the need for controlling of hazardous energy or using alternative measures in order to protect the employee. Once again, put those same hazard points that the guard was put there to begin with. Peter Koch: Nice. I think that's a good framework to start with. So, when we look at a machine, we've got to look at where those hazard areas are, where there could be accidental contact and those should always be guarded at all times. And then if we got to remove it, then another process has to be in place to protect the employee. Perfect. So, what industries or job activities need to be aware of or understand machines safeguarding? Hartley Webb: It's really all industries. It's amazing. The different jobs you could go into where people won't think that there is a need for safeguarding. But I mean, typically we think about the metalworking industry, the woodworking industry. I mean, food processing that I deal a lot with has a lot of need for machine guarding because again, there's a lot of material. I'm sorry, a lot of machinery that's handling product. The printing industry has as a strong need for machines safeguarding course. You have completely different exposures in the agricultural industry, in the forestry industry, and you could even include stuff like even grounds keeping industry where you have a lot of that mobile equipment that still has a lot of requirements for machines safeguarding. But I've helped businesses from, you know, retail, wholesale. I mean, is conveyors in a lot of different businesses. Almost any business has some type of either small power tool or something. It's in the maintenance shop or groundskeepers’ shop or whatever that that could bring about the need for safeguarding. Peter Koch: Nice. So, every industry, like you said. So, it doesn't matter where you're at. Could be a. Mom and pop business. It could be a multi-national or multi-state corporation that has a lot of different functions, but every industry, if you've got a machine that has moving parts, you've got a more than likely you'll have to have some machine guarding on it, whether you have to install it or there comes that way from the manufacturer. Would that be a fair statement? Hartley Webb: Yes. Yes. Correct. Peter Koch: Awesome. Ok. So when we start to look at our machines and especially our older machines, or we found this to actually in the recreation industry, when we're purchasing a piece of equipment from overseas, they don't always have the same safety standards that we do for production. And if you don't know and you know, ask for it, parts may not come guarded to the extent that we expect them to be in the states. So, when we're looking at a piece of machinery, what are we looking for to determine whether or not it needs to be guarded? Hartley Webb: Again, you're gonna be looking for those common hazard areas to start with. You're gonna do like an assessment. Well, the first one we'll be looking at any rotating motion. Are there any shafts? Are there any surfaces at all that may be rotating where you could either get pulled into some type of day nip point like in running net point, which we can talk about more. Is there any reciprocating kind of motions that are taken place where you could have a struck by or a pinch type exposure? Are there any transverse motions that would be something you would find them like chain drives or belt drives where you would have, you know, transverse motion or, you know, surfaces moving in opposite directions. Anytime that happens, typically you will also create a nip point type hazard. We'd be looking for any like points of operation where you would have a cutting action that would be taking place or punching, shearing or bending kind of action where there's the potential for a part of the body or something deep to get caught into that hazard area. Peter Koch: Okay. So, you mentioned rotating parts in running nip points, transverse motion like a chain drive point of operation cutting operations. So, as you're assessing your piece of equipment, first of all, you'd be looking for moving parts. What those moving parts are doing, are they rotating? Are they driven by a sprocket or a socket? And then can you touch those points? Right. So, I guess if you can see it, does it mean that you have to guard it, or do you actually have to be able to contact it? Hartley Webb: Well, no, you don't actually have to come in contact with it because I mean, a lot of those actions that we just spoke about were, you know, hazardous activities that are taking place. But you could also have the potential for falling into walking into or struck by of material, you know, coming off of the machining process due to failure. And there's a lot of equipment that requires just like a debris shield would be required in a lot of pieces of machinery that’s actually classified as a guard. And a simple example, that would be something like a milling machine or a blade where there are rotating motions. Some of those can't be physically guarded on some of the manual type machinery but would have like a barrier debris type a barrier to prevent access, but also a to prevent contact with any debris that may be coming off of the point of operation. Peter Koch: So, in the… Hartley Webb: And also, we also didn't include heat would be another one. So, if there's any hot surfaces, I mean, that would be a different type of exposure, but that would also bring about the need for, you know, for safety. Peter Koch: So, any hazardous energy that you could be exposed to there, looking for it to be guarded from accidental contact, like you said, from for the employee. OK, so a debris shield that be something to look at. Let's go back to those different types of points and let's talk about those in running neck points. I know that's a question that comes up all the time. Describe for me what that in running nip point is and what are the hazards around those? Hartley Webb: Again, it's probably one of the from my experience, that has been the hazard that has caused them the greatest amount of both severity and frequency of injuries within the industries that I work in, the food products, wholesale warehousing type, where there's conveyors that in running nip point, it can be created in several different areas. But typically, it's like a belt coming in contact with a rotating drive wheel or tension wheel. You're going to find those on a conveyor system. You're going to get those nip points created on any type of conveyor, whether it be a chain conveyor, a belt conveyor or a roller compare to inward moving wheels in opposite directions like you would have on a on a conveyor roller conveyor type thing has that potential. At the end where you could come in, where you get two adjoining. Systems where they could get pulled in. But the most common ones would be a belt and pulley, a conveyor rotating or drive wheel or tension wheel along with the belt. Even in a transverse type of belt, the hazard where again, if part of your clothing party, a body or even a tool or something that you're working with or a piece of the product that's moving on the conveyor that has a possibility or on a machine that has the ability to get caught, which could then inadvertently pull you or injure you if you're standing nearby when that takes place. Those types of hazards would have to be guarded against that occurring. Peter Koch: Ok, I'm gonna ask you here to give me an example. So, can you frame for us and kind of give us a picture of what type of machine would have an in running nip point and kind of describe for where and how that might expose the worker to that energy? Hartley Webb: Yeah, probably the best scenarios would be a chain and sprocket. So, where that chain needs that dry sprocket on the in running portion of that, obviously there's no hazard on the outrunning but that in running would have to have protection. So rather it's a belt pulley or a chain sprocket. Typically, would be found on some type of power transmission or derived system that would have to be guarded or that portion would have to be guarded so that you cannot make contact that would draw you into that hazard area. Peter Koch: Gotcha. Perfect. So that makes sense. So that the section where the sprocket or the drive wheel is coming in contact with the chain or the belt typically really at the bottom as it starts to pull that in where those two pieces come together. That's that in running that point. That's what you're talking about. Hartley Webb: Correct. And there's almost nobody around that has an experience that was like a bicycle where your pant leg got caught onto that in running neck point of that chain and sprocket on your bike. The only difference is when we're dealing with industrial, we have motors behind that energy. So, the rotation doesn't stop. And that's where you could it could have some serious injury from basically continuing to draw in, you know, the clothing or the body part. Peter Koch: Sure. That makes a lot of sense. I think that's a great description. That chain and sprocket for the bicycle and I. Yeah, everybody has written a bike has had that. Has that happened before? But the benefit of the bicycle, like you said, is it will stop if you get too much, too much in there or you just fall off. But the machine's not going to stop it until someone pushes the button or until it reaches its maximum tolerance. OK, so in earning the points, we've talked about those another rotating part. You talked about rotating shafts. So, there's a lot of rotating shafts that are out there. What part of that shaft has to be guarded? And what are the guidelines around what has to be guarded for that rotating shaft? Hartley Webb: Yeah, the if it's a shaft itself. Well, I guess this first we'll talk about the shaft. And so if you take a shaft and connect it to some type of the pulley or a gear or something like that, there's potentially going to be an exposing shaft end like you would find on a like a grinding wheel where you'd have that shaft coming through the center of the wheel. And then on the outside, you would typically have like a hex knot or in that same thing's gonna be in an industrial facility, may or may not have a nut on the end of it. It could just have a set caller on the end of it. It's connected by some type of this that screw with or without maybe a keyway. So that shaft end that has some very specific requirements to it. If it doesn't have any burrs. If it's smooth. If it's less than one half the shaft diameter. What's sticking out of the of the surface that it's uprooting through? So, one half the shaft diameter or less, you can leave it alone and don't have to safeguard it. But if you're going to let more than that stick out, if it has any exposed keyways or if it has a collar with a set screw on it. In that set screw is sticking out so that it might it could come in contact with clothing or be able to catch something that now has to have a guard on it. Hartley Webb: So, the shaft and is one of the areas you'd want to focus on. Anytime you have any type of the shaft on a piece of machinery, then the shaft itself you would want to be taking a look at to see if it's an extremely slow-moving shaft. And I can't remember exactly the rotation. It is in some letters of interpretation that have been documented. But if it's really slow, I mean, slow enough that you could almost sit on the thing and, you know, get off of it without it moving more. I mean, if it's really moving slow, it's not much of a hazard, but it fits. But if it has any rotation to it, it could accidentally catch clothing or catch material or hair or anything like that. It's going to have to have some type. The shield on it. If it has a keyway in it. Now we have a surface. It can easily catch material that has to have a guard on it. So, if your shaft has an exposed keyway, it's gotta be guarded. If it has any rough surface, it has any anything on it. All set callers or anything that could do again could catch clothing, hair or strike you as it rotates. It's going to have to have a guard on it to prevent contact with that hazard. Peter Koch: So, a smooth shaft that's greater than one half the diameter of the shaft itself. That that much is sticking out beyond the machine that is protruding from if it's smooth. No keyway. No castle. No. No set screw. Totally smooth. No damage to it. Does that have to be guarded? Hartley Webb: If it's less than half the shaft diameter total sticking out? No. As far as size and in it in its protrusion. But again, looking at it like you just mentioned, any of those items that could accidentally cause you to get caught on it. Hair, clothing, or even as a struck by if it's coming around, you can catch the body. It's going to have to be safeguarded. So sometimes we'll try to eliminate the need for a safeguard by cutting those shafts back. There’re no exposed keyways, no exposed set screws. So therefore, the shaft can be left unguarded. Peter Koch: Very good. But if it is longer than half the diameter, then it's gonna have to be guarded regardless or if it has any protrusions from it. Those are all good to remember. OK. So, you're looking at are the rotating shaft ends. Those are some good points as a have something that's going to catch the person, their clothing, their hair, a tool or strike someone as it comes around. Then those have to be guarded. The length is something you have to look at. Any you brought up a good point, too, that you don't have to guard it. If you can make it shorter than half the diameter of the shaft itself. So, you can if it's possible to cut it back, you can cut it back and therefore eliminate the need to do that. So, it's another tool in your box as you're thinking about machine guarding. Hartley Webb: Correct. Peter Koch: Excellent. Hartley Webb: And a good example of that would be like a buffer. Put a buffing wheel on like a bench grinder but use a buffing wheel again. The guards could come on the manufacturers guards can come off because of the buffing wheel and you may need the entire surface. So, if you need the entire surface of the wheel, you can justify the removal of the barrier guard. But you still are gonna be required to guard that and that. And you're still going to be required to guard the shaft. If there's an expose shaft between a motor housing and the buffing wheels. So that stumps a lot of companies that just want to have an open buffing wheel. But they still need to either have a smooth, not smooth cap on the end or they're going to have to come up with ways of guarding the end nut along with the drive shaft. Peter Koch: So that's another option there. I was thinking that as you described that I'm thinking about the buffing wheel that I've used in some woodturning shops for two to two polished finished products. And some of them have three or four wheels right on the shaft itself that comes out. And at the end of the shaft is machine. So, the last buffing wheel stops right up against this. So, there's nothing sticking out. However, if there was something, stick it out. You can put a smooth cap on the end of that too, then. Hartley Webb: Correct. Usually that's usually that's a hex nut on that end. And oftentimes my counsel machine, a smooth almost like an acorn nut without any hex fittings on it that will actually get rate over that in fitting or if you're a connection point. And so now that you get a nice smooth shaft, it doesn't stick out more than half the diameter. They can now leave that out there in case they have to use the entire surface of that blast buffing wheel. Peter Koch: Perfect. Without putting a large guard around that to prevent contact. Okay, that makes a lot of sense. Yeah, very good. We talked about the ends of shafts. When does a shaft itself need to be guarded? Hartley Webb: Typically, is when you have access to it. I mean, again, this is going to be every industry is a little bit different, but a lot of places can guard by location, which we can get into. You know, the methods of safeguarding. But if you can't have access to it, you can't you know, if you tried to reach it, you cannot with the full arm's reach, gain access to it. Then, you know, you can have basically administrative procedures and say, look, you need to go in. That area is going to be basically you'd have to control hazards, energy prior to entering. So, it can be guarded by location. Oftentimes what I see is it's where the operator station may be and they have that again, the potential for that accidental contact where clothing or something that could drape like hair, could drape over that rotating chair. And in that case, you're gonna have to guard or put a guard on to prevent contact. I mean, that's gonna be the same as any revolving surface or rotating motion that we talked about initially as a hazard. In the end, a lot of times in our mind, we're thinking of that horizontal shaft. But if you think about rotating motions, the one that most people can reference would be like a chuck on a drill press that has to be protected against accidental contact of that rotating surface. And that's no different than a chef would be. Peter Koch: Yeah, that makes sense. I was thinking, as you're talking about, that actually a vertical rotating shaft back in my history of employment, working in the recreation industry. We had some large vertical pumps for snowmaking systems and the older pumps had a vertical rotating shaft below the motor that went down to the impeller into the pump pit itself. And that was exposed. So, once it started up, you could easily come in contact with that. And in one of the first places I worked, it wasn't guarded initially. It did get guarded after a while. No one got no one touched it because no one was allowed into that area except the operator during operation. But still, that's the way it came from the manufacturer, or at least that's the way it looked like it came from the manufacturer as a 22-year-old working snow making for the first time. Hartley Webb: Something like that, there's basically the two most common ways would be to put a fixed guard over it so that you don't have access to it. And some of the most common methods that I see in the woodworking industry is and what actually in a lot of industries. But to put a slip collar over it, which is basically like a piece of TVC pipe, one size larger than that rotating shaft, kind of works like the shaft on a PTO for a like a farm tractor. When you're using an implement behind it, you'll put a slip shaft over that. So, in the event that you accidentally come in contact, land on it, your clothes drape over it, that the shaft, if it is rotating, may actually mean the covering like the TVC pipe. You could actually grab that pipe and the pipe would stop at the shaft but continues to spin inside it. You don't have access to that rotating surface. So, a lot of times I'll see those shafts like that just with a simple slip bag placed over it. And know that works effectively as long as it's installed properly. Peter Koch: Excellent. That's another really that's another really good point. So, we've been talking about a number of different ways to guard. So. you talked about slip collars. You talked about a fixed guard. You talked about a smooth cap on the end of a rotating shaft. What are some other ways that you can guard some of the machine guarding hazards that we've talked about so far? Hartley Webb: If you looked at it from a compliance standpoint, the one that they the one that compliance really likes to look is a fixed guard. So, the best guard is an actual fixed, solid fastened down, you know, some type of guard measure that protects you from that hazard area. If so, if you can't put a fixed guard on it, can you put an adjustable? So, an adjustable guard would probably be the next guard. So that's something that maybe manually would have to be adjusted each time a machine or something was used. But again, that would be the next level. So, you've got fixed, you've got adjustable. Then you would go to like self-adjusting. You know, where that would be like in a lot of the machines or saws where you thought of your table saw and you put some of the standard guards at table saws have that's gonna be just self-adjusting guard that just it just itself to the stock as it's being fed in. Obviously, the hazards of that type of guard is if you can continue to, you know, pass a part of your body in there. The guard is going to adjust into whatever is being fed into it will adjust over it. It really just protects you from having that accidental contact coming in from the side or above. But so, you've got fixed, adjustable, self-adjusting, and then the next level would probably be like an interlock type device that would be on some type of a fixed barrier or a door or gate that might be around the hazard area. Hartley Webb: Then you're then at that point you'd probably be looking at devices and without getting into a lot that we can get into some discussion. But basically, there's like six common devices. There’re those present sensing devices that will sense when you're in the area and stop the machine or prevent access. You've got a safety trip device where again, that's going to trip, he just stops the machine or trip some safety measure that will prevent access to the hazard. You have two-hand control. There’re basically two types of that two-hand trip and then two hand control. So, two-hand trip with the you know, you put your hand somewhere, the machines. But then they let you remove your hands and do something else where a two-hand control, you'd have to leave your hands in place the entire time. The machine's functioning and if you remove your hands, the machine stops. Then there's pull back and restraints, which now I've actually got the employee somehow harnessed where each time the machine cycles, it literally pulls their body out in a way from the hazard each time that machine does a hazardous activity at the point of operation. Or you can have restraint. That's basically just putting the person on a on a tether that prevents them from reaching a hazard area. So, if we go to that, it's fixed, adjustable, self-adjusting, interlocked. You can use your devices than the next one would probably be by location. So, in the world of safeguarding, if it's above seven feet from a walking, working surface, it mostly doesn't need to be safeguarded unless for some reason an employee elevates himself. Hartley Webb: Then it would have to be addressed or taken in. And then there's some standards about fast moving belt's large belts and stuff where it still protects in the event of the belt breaking over your head. But pretty much you can guard by location and that's kind of a 7-foot rule. Then obviously you could use stuff like robotics and stuff to remove the human out of the hazard area and auto feed type systems, so the employees aren't involved with the hazardous activities. And then it really goes into administrative where that's just using everything we just discussed. But that's including the necessary signage as an awareness, installing some type of, you know, barrier that you would have to go through before you get to even some of the guarding. And that would also include the employee training, training on what the guards are, what the signs are, what the do’s and don'ts are, along with the machine and the use of the guards and the injustice, some the guards. So, it's kind of a little toes were nine kind of key areas. But if you're doing a guarding assessment or if I was to come out and do a guarding assessment on a machine, I'd be basically looking at how many and which one of those nine items could potentially be used to safeguard that piece of machinery. Peter Koch: Great. There's a lot there. Looking at a piece of machinery from each of those places. But let's talk about some of the benefits of or the drawbacks as well for each of those. So, let's take them kind of in turn. So, the fixed guard you stated the benefit before of the fixed guard is it's fixed. It's in place. It's always there, protects the employee. What's the drawback of having a fixed guard? Hartley Webb: Well, the only drawback would be it's a fixed guard doesn't work for you. So, in other words, you need to have access. Product has to flow under it or through it, then obviously would be in the way. Or if you have to have visibility, sometimes a fixed guard can be an issue. The other thing with a fixed guard is depending on again your operation, you may not be able to install it. Fixed guy. Due to the hazard. It's just it's not physically possible. Example of that might be. See, you've got a conveyor system and that conveyor is two or three hundred feet long, which you actually install a solid fixed guard for the entire length of the now 200-foot-long conveyor. Or do you just guard the high areas of exposure such as the nip point and stuff, but yet you still have a moving belt system. So then they would let you go to another like a trip kind of device where you'd use like a trip wire or something like that, where if you were outside of those in running nip points and stuff that have physical guards on and that's where you've fixed guards would be located. You'd also be using alternative measures in lieu of completely encasing, you know, the piece of machinery so you can't get access to it. Peter Koch: So, the trip the trip wire or the trip guard be in addition to having a fixed guard then, is that what you're saying? Hartley Webb: Correct. Yeah. Because it's interesting because the most commonly not to get into citations is that the most commonly safeguarded violation is the one that says basically a machine needs more often needs more than one type of guard to be safely protected. I can remember exactly how the standard reads, but it's read at the very beginning of the general requirements for machine guards. And in you know, people sometimes just stop at implementing one guard when they really haven't addressed all the hazards of the machine. And it comes back to that point that the entire machine needs to be assessed. And what are there all the potential hazards associated with that given machine. So again, it will oftentimes need more than just one. But the other common one that a lot of accounts that I work with, a fixed guard tends to build up and accumulate debris. So, if you have like conveyor systems or machinery that has the ability to produce a lot of debris. Then those fixed cards can become a hazard because they lead to more maintenance type activities for having to do cleaning, which now is going to expose you to hazardous energy and elevated issues and, you know, elevated fall exposures. So, companies won't go with a fixed guard. They'll tend to go with area guards or barriers that going to keep you away. So, they tend to guard more by location and then allow the machine to run so that it doesn't have as much downtime for cleaning. Peter Koch: That makes sense. And so, a couple of points that I wanted to highlight from what you just said was that the entire machine has to be assessed and not just from what moving parts it has, but what moving parts does it have, and where will the employees or where might the employees get access to it during the course of normal operations? So, if they have to walk behind it, to walk around it, move above it. Do something with it, even if it's not in the point of operation area for the machine. If, say, the back of a powered press or something. You have access to it because you've got people walking back and forth. That area might need to be guarded just as well. So, in your assessment, you're not just looking at where the operator is, but you're assessing the entire machine. I thought that was a really good point that you brought up there. Hartley Webb: Correct. And probably almost anybody listening because either you don't care if it's a push mower or more or riding more. But everybody is familiar with like a riding lawn more. Well, if you looked at the guarding that's on that you have guarding on your power transmission. So that drive system that built pulley that has to be guarded. You've got your point of operation. You're cutting deck. The guides that are required on that to keep debris and stuff from being thrown out from the sides, along with the discharge chute in the stickers that are on that lawnmower are riding more from the manufacturer. Those are administrative controls. That signage is part of that guiding requirement. And that's something I often see in the agricultural industry where they'll have older tractors that they've repainted them or they've just from where. And those stickers that are on the rear fenders of the tractor, on the operating controls of the farm tractors that may even be attached to the PTO guarding mechanisms, those stickers have to be on there. They're part of the manufacturer's requirement for the safe use of that guard, and of the tractor. So that becomes part of that guarding that information of what are the hazard points and what to stay away from. Along with the actual physical fixed or adjustable God's. Peter Koch: Perfect. Perfect. So those stickers or the information parts are a part of their machine guarding requirement to giving instructions. Awesome! Hartley Webb: Correct. Peter Koch: Let's talk a little bit then about the pros and cons of those adjustable or self-adjustable guards. You talked a little bit about that. How? There's a couple of cons for the Self-adjusting Guards. But give us a little more insight into the pros and cons of using an adjustable or a self-adjusting guard. Hartley Webb: Well, the self-adjusting, that's just the maintenance criteria. So that has to basically be maintained so that it's functional and operating in the way that would that it was designed to be adjustable. Good is where I typically would see or we do see a lot of exposure areas because again, that comes back under the training of the employee, which is, you know, one of those administrative requirements. It's also part of the company's safeguarding effort. But there is a guard opening scale. So, it pretty much represents the human arm. So when you're adjusting any of those adjustable guards, they should be adjusted in a manner that in the event that your hand was to pass under that guard, you cannot make contact with that point of operation, with that hazard activity is taking place. So, you know, you can have that opening can become larger and larger the more you come away from the hazard. And once again, it represents really it represents the human hand. I think it goes down as far as a quarter inch. So any type of an adjustable, if you want to think of like a table saw or a band saw, which probably most people have at home or in the work, is that guard can't be graded in a quarter inch from the largest portion of the stock feature that you're feeding into the machine. So, you would want to be adjusting that all the time and keeping that within tolerance of the part. So, again, it comes back to a human requirement and knowledge to keep adjusting that. That's one of the biggest downfalls of that adjustability, is it doesn't get adjusted as much as it probably should. Peter Koch: Yes, you kind of put it in an either in an average spot, if you adjust it for the largest piece that you're going to have and then you start feeding. Pieces into the machine and you don't adjust it back down. Therefore, exposing the employee to that, that the hazard of the rotating parts of the moving parts inside the machine, that makes sense. So, comebacks that the human factor is the challenge with the adjustable guard. Sure. So, what about interlocks? I know quite a few of the machines that I've worked with before. You open the door. The machine stops. Or you know, you can't operate the machine again until the interlock is closed. Are there any there? There's a really great benefit for that. Like if there is a door that is enclosing all the rotator part, rotating parts or moving parts like a CNC machine. Another piece of machinery, you might have a window where you can see into the operation itself, but in order to access, you have to open the door and then the machine won’t operate until it's close. Great control, great guard. But what are the challenges that we might have with an interlock system as a guard? Hartley Webb: Well, they're allowed to be used. The biggest thing is, again, maintaining and making sure that they're actually functioning. Unfortunately, they have the ability to be overridden by the employee often times or, you know, shouldn't be, but they can they can make it so that the interlock is no longer functioning, either by turning it off, by putting some type of the mechanism in it that bypasses it. Obviously, that would create a very unsafe situation because now you wouldn't have a secured guard. And basically, it's just it's taking a fixed guard, making it easily removable or allowed to open. The other thing that it brings about the need for, which would be another conversation for another time. But again, once you open that guard, even though it may be interlocked and shut down or stop some functioning part of the machine or the hazard area, you still have to deal with the control of hazardous energy. If what you're about to do is classified as a service or maintenance activity, which typically would be the reason you would have to go beyond that, that guard. So, it's there, too, as a protection measure. But going beyond the interlock brings about the need for control of hazardous energy. At that point, we'd have to say probably ninety nine percent of the time. Peter Koch: Yeah, that makes a lot of sense. Makes a lot of sense. So, we're gonna take a quick break and we will continue with some more discussion with Hartley on the back side. So, we'll see in a moment. *********************************************** Peter Koch: Welcome back to the Safety Experts podcast by minute. Today, we're talking with Hartley Webb, safety management consultant at MEMIC. So, let's jump in with some more questions. Part of the break, Hartley, we were talking about the different types of machine guards and they're pros and cons and we talked about fixed, adjustable, self-adjusting and interlocks and now we're onto those devices. So why don't you talk to us about the devices and what the pros and cons are for those devices? Hartley Webb: Ok. Well, the first one would be the first one that comes to mind would be like a presence sensing type device. And there's a lot of different ones. Some of them there might be a sense mat on the floor. So, a few that can be wired either way say that the they want you that you want the operator to stand in a certain area and not leave that area so that they don't become injured. You can actually put a man on the floor that would be interlocked back to the piece of machinery. But you can have one or two ways. Either somebody steps onto the mat trying to enter into an area that would that would activate safety devices, or you can have it so that the employee literally has the standard or be station in one area in in order for the machine to function. So that's one type of present sensing devices. Other ones would be the most typical one. Probably people are familiar with would be like curtains or some type of barrier interlock where it senses some part of the body entering into an area. And when it does so, once again, it either sets off alarms it could it could stop the piece of machinery. It all depends on what the machine is and how close you are to the hazard area at that point in time. But those are good examples of present sensing some of the downfalls, short sides of those. Once again, they have to be maintained. So, people have to test them. They have to make sure that they're being serviced properly aligned properly, are given on what type of device that they're actually using. Peter Koch: How often... let me interrupt you for just a second, Hartley, how often do they have to be tested and evaluated, those present sensing devices? Hartley Webb: Most of it's going to come back. When I usually do that, I usually look for the what the manufacturer's requirements are for like a light curtain. So, in some of that may also be based on how dirty the environment may be. That may affect the sensors or the photo portion of the of the sensors. So usually I go right to the manufacturers literature to find out what they have. I believe OSHA’s got some requirements for like curtains. And I think that's only when used on presses that they do have some requirements. And I want to I want to say that's like a, it's like a pre-check where you'll just verify that the system's working based on its light mechanisms, where it's got a red or green to show you when it's been tripped. As far as maintenance, maintaining them and keeping them within the tolerance that’s required, that will go back in manufacturer's literature and following that requirement. Peter Koch: Ok, good. And all those can be adjusted based on the machinery. How far away? How big the thing that you want to identify is as it comes into the presence of whatever you're trying to, whatever you're sensing. So, whether it be a light curtain or the mat, all those tolerances can be set. So that can be tuned pretty well for really good safety or in good safety and efficient operation as well. So, you've really got to know what the manufacturer says about how to adjust it, when to test it and how it's supposed to function. Good. Good points there. Thank you. So, from there, from the other devices you had mentioned before, you had mentioned safety trips to hand controls, to hand trips, pull back restraints. So, what are some pros and cons of those different devices? Hartley Webb: I shouldn't say I've been fortunate of, I’ve been unfortunate, but I've been able to do some accident investigations where they used a safety trip. And once again, the safety trip just it's a two-hand trip. And sometimes you can actually have a one-hand trip if you want to use buttons. So that basically controls either one or both hands. So, you're able to control where the operator’s hands are at the time a piece of machinery starts. The difference between two-hand trip and two-hand control that I spoke about would be the control they would have to leave their hands on those two pressure points doing the entire cycle of the machine. Usually that would be used in the event that they could take a handoff and reach into the machine and still be injured. So sometimes you'll see just a control use just to like to shut a gate. Once the gate closes, you're able to let off the control and the machine can cycle. Other types of trips we had mentioned earlier would be your trip wires. Sometimes those run along the length of something like a conveyor. I also have a lot of industry where they'll use them to surround a piece of machinery such as a roll press, say, in the metal industry where you could be anywhere around that machine, 360 degrees. And if things are going if things aren't going right or there's a hazard anywhere, then you can quickly basically the trip wires down by your foot and allows you to quickly step on the wire on like a roll press that would basically stop that machine immediately or like on a conveyor, you would be able to pull it. So, it has a lot of various is a lot of different type trip devices. It can put out there. It can be out there, but it and it just allow some allow actually another one that's very common is device where you'll see it in a plastic or in the rubber industry, sometimes in the textile industry where if you accidentally get caught in a machine because you have to have the operation has to be open to gain access to the product. But if something happened, then you were to fall forward or you get caught on a product and got pulled towards a machine, you would come in contact with some type of either a swinging overhead bar or there'd be a bar crossed in front of you. That when you make contact with that, it would stop the machine prior to entering. Probably the one that most people would be familiar with that aren't into some of those industries would be if anybody is looked at like a woodchipper, they have one of those bars that would be a trip device where if you get caught on a tree limb and it started pulling you into the chipper, you would just reach up a party of body and hit that bar by the feet you and that would stop the feed mechanism. Peter Koch: So, it's a change your pants bar, pretty much because you're saying later, if your heart is going a million miles a minute, because you're just moments away from being incorporated into whatever product you have. Holy cow. Yeah. Peter Koch: So, question I have on those trip wires, though, those by themselves, are they considered an effective guard, a trip wire by itself, or does that have to be used in conjunction with another type of guard? Because it seems to be more of an emergency stop device that I would have to physically trip that. Like I'd have to reach out, I have to touch it. I'd have to kick it, but I could step over it or I could move around it. I don't actually have to touch it. So, can you use it trip wire or as I guess as you stop wire or something like that as an effective guard or would it be used with something else? Hartley Webb: I've almost never seen it used by itself. I can't think of any machinery where it would be the sole type of safeguarding. Usually it is used along with like an emergency stop button that would probably be at the operators control area. So that would be the primary emergency stop. And in the event that the operator walked away from the control panel. He's got access to that trip wire. That's what you would typically see on like if I go back to that, that roll pressed for steel. Right. But it's you know, if you'll start if you think about it on conveyers, which is probably where it's most predominantly used. Again, I go back to that statement that, you know, more than one method of safeguarding. And if you take here, you know, you take a conveyor. There’re all sorts of houses associated with that that need to be guarded. So, you it's going to have to usually be used along with fake guards, adjustable guards, interlock guards. I mean, every machine's different, but I've never seen it used just solely by itself. Peter Koch: So, the bottom line that makes a lot of sense. The bottom line is the guard that you have must protect the person from accidental contact of rotating parts or moving parts. So, it must be it could be a single type of guard or more than likely because of the complexity of the machinery. It might be more than one guard. And that example that you used of the riding lawnmower and the number of different guards that it has that has multiple different guards, has it just adjustable guards, has fixed guards and administrative controls on that to help protect the operator. So that's a really good description. I think a good rule of thumb going forward. Don't just think that one guard is going to do the trick. Really do the assessment and evaluate how can that employee common accidental contact with the moving parts that we've identified. In your travels around and again, working for MEMIC for so many years and then being in heavy industry prior to that? Hartley, in your experience. What's the most overlooked guarding exposure that you see? Hartley Webb: I have a lot of heavy industrial accounts that I tend to service, but it's not necessarily always heavy industrial, but the conveyor which we've talked about is for the most. Serious accidents that I've had to investigate from the frequency associated with people getting caught or injured when there's conveyors in the area. But I mean, I have conveyers in my warehouses to move freight around. I have conveyers in my food processing areas again to move product around. I mean, there's conveyers in the printing industry. There’re conveyers in the agricultural industry again. I mean, I don't really think there's not I don't think there's an industry out there are many that doesn't somewhere have, you know, a conveyor type exposure unless you're maybe the service sector. But I even have those in some of the back storerooms and stuff for a receiving area. So, it happens that conveyor. There's just so many things on that conveyor that have to be addressed as part of that. You know that machine safeguarding assessment. Peter Koch: That makes a lot of sense. I'm thinking as you're scrolling through all those different industries and I'm looking at some of the industries that I work with tend to be on the softer side of the service, retail, hospitality, recreation. And even there are guards looked back at the house from a food service standpoint. And you have multiple pieces of equipment that might have a conveyor like an automated pizza oven will have a conveyor to bring raw product from one side to cook product on the other side as it moves through. There're other conveyor systems that might move pizza or move dough from one area to another or through a platen machine to flatten it out in the recreation industry. What's becoming very popular to move people from point A to point B are carpets, magic carpets. So, think about an escalator without any steps. Right. So, it's just a basically a conveyor belt for humans. But you still have to maintain it. And there's been numerous injuries for people getting caught either trying to maintain and clear it from snow or debris or they're actually underneath it. And it starts up so a little different from a control of hazardous energy. That's the lockout tagout thing when you're in a maintenance process. But they still have to be guarded. So, you're right, they're all there all over the place. So, don't forget the conveyor. Hartley Webb: And you're going to have a, yeah, I kind of have a list of, you know, some items that if I'm looking at a conveyor, the first thing I'm looking for is the things you just talked about of those big ones, that that that's what I'm looking for, those fixed guards. So those nip points, those rotating surfaces, where can those where do those areas exist? Typically, on either the beginning of the end of the conveyor, we'll get that in running nip point of some stationary surface in the conveyor or can I get into the conveyor in between the two transverse motions where I can come in contact with those wheels or the drive wheels? You know, the ease or the return mechanisms. So those can be protected by fixed guards. If they do have some emergency stop mechanism, I usually ask that that has some type of a requirement for resetting before any type of resuming of the conveyor operation. So, if somebody does hit an emergency stop, just basically pulling that stop button back out will not restart that equipment. It's going to take some type of manual resetting to occur. I'm usually looking at protection from walkways. You mentioned that earlier. If somebody is going to walk alongside the conveyor, that's when we would look at the trip wires or you use some type of fixed guard if it's a possibility. How about those people that pass under a conveyor or have to pass over a conveyor? Again, if it's over the conveyor now, we would have the need for the fall protection or the railing system to keep access from landing on the conveyor. If you're going to pass under a conveyor, what type of overhead protection exists? Warning signs that we've talked about in the past, it would be on all of those hazard areas of the conveyor. So, is there signage there that explains the hazard? It signifies that in running nip point or whatever there has, it might be warning light stuff's going to either restart, start back up or is in operation. So, people realize it has that potential for either automatic restarts or manual restarts. If there's an opening through walls and floors in a building, you know, then that also has to be, you know, if you have access to those areas, can those create hazards? Do those need to be to be safeguarded either by location with some type of a barrier or whatever may be required? Guarding of star buttons for a compare. So, you don't get an accidental starting. So, it is either the star buttons have covers or the start buttons are recessed or some type of a sequential series of buttons that have to take place in order for a conveyor to start up. It's not just by pushing one single button where you can get accidental start up of the system. So those would be some of the things that I would look at along with his capability of being locked out during servicing or it's to be shut down, what's the process for overloading or jamming and that kind of stuff? So those are just a few of the simple things are the key things that I tend to look for any anytime I see a conveyor in any of those industries. Peter Koch: Well, I was just trying to keep a list of all those things that you are going to look for. And I couldn't keep up. So, if I'm looking after I listen to this podcast, then I'm looking back out on my factory floor and I'm thinking about, gosh, look at all those machines. We haven't done a machine guarding assessment or maybe we have, but we've changed some of the tooling. We've changed to the machines or the configuration of our shop. What are some resources that we can draw from and what are the standards that drive the requirements for machine guarding? So, let's take standards for. So where can someone find the standards and what are some of those standards that drive the requirements for machine guarding and then we'll talk resources. Hartley Webb: The best place to go to the standards would be to the most up to date would be to your ANSI standards and stuff. But OSHA has a lot of great publications that that really help out with machine guarding and they've really broken it down. You talked about like conveyers, which I just went over. There's so many different exposures on conveyers. Those are actually specifically addressed in the general industry standards, in the construction industry standards. And I believe they're even individually addressed in the marine standards. But you have it in general, in industry if you wanted to go to the OSHA regulations. Subpart O in your 1910 and your general industry regulations. Subpart O will cover all of your standards for machine guarding in the general industry. And they're very specific. It's very well broken down where they have a they have a section just dealing with the general requirements and then they get specific into all your woodworking tools, your abrasive tools, you know, your steel presses, forging machines and power transmission. So if you're actually looking at a power transmission type exposure, where it goes back into what we talk about, shafts, pulleys, we didn't talk about open flywheels, but if you have an open flywheel, is it a belt running through or even a sprocket maybe part or a chain maybe passing around? Again, you have to protect those openings, or those exposures and you've got a very specific standard so you can go right to the standard and that defines exactly what you can do. Hartley Webb: Your construction standards, Subpart I. So, in your general industry. Subpart O. and your construction is subpart I. Actually, addresses them with the tools, handheld and power tools and it gets into all again, it talks about almost the same standards for your woodworking, metalworking, power transmission, that kind of stuff. And if you looked at your Marine standard, your 1915, it's also found under this subpart H, but that's also your tools and related equipment and that gets into abrasive and again, some of the tools most commonly found in that industry. So, Subpart O, general industry, Subpart I construction and subpart H for your marine industry. Peter Koch: Oh, fantastic. So, it's a good place to start to look at the compliance side of things. And I give you the what and the where for. So talk to me a little bit about the different resources that might be available to someone who would want to do a machine guarding assessment or to put a program or a plan in place at their business or work and they turn to for some resources. Hartley Webb: Once again, I tell most of my accounts or businesses that I'll come in contact with that OSHA has some great resources and they have a they have a lot of what they call E tools. And if you can go right to their Web site and look for E tools and they have them for all of the woodworking and all of the metal working. And they also have a general some general ones that get into your power transmission and conveyor type systems in their great assessment. They're really easy to read. They're in bullet format. You can go right down through. And it kind of describes exactly what the guarding requirements are for those specific pieces of equipment. And they've just taken their standard. But they've actually they just made it easier to read, easier to understand. And some say you can almost use it as an assessment form when looking at a piece of machinery. Peter Koch: Perfect. So, the OSHA standards for looking at compliance and then the E tools for helping you with the different assessments that that you might need to do. Awesome. Any other resources? Hartley Webb: I mean, if you're looking at somebody, ask me about a specific machine and that's a machine that has been fabricated. I usually will want them to address or I'll go look at the manufacturers' literature for that machine. So, what does the manufacturer say is required? And you can when you started, you kind of mentioned that early on. That's a good reference point, but it is a lot of documentation by OSHA that is stated. The fact that the manufacturer of that equipment isn't responsible to install all the necessary safeguards. It's the employer of the person who purchases that equipment that has to identify is there an existing hazard? You know, you begin using this piece of equipment that I may need to add additional safeguards to in a great example of that is like a bandsaw. You can go out tomorrow and buy a vertical bandsaw. Yeah, vertical bandsaw. Almost anywhere being bandsaw to cut wood with. And there's no guarding requirements on that bandsaw does not meet the standard requirements. So you would basically you go in to the standard for a vertical bandsaw and it would describe the you need to have a guard on that machine that prohibits access to any part of the blade other than the part that's being used to cut the product. So, but all of those bandsaws are fabricated so that you have access to a lot of the blade above the point of operation. And that has to be protected by the employer prior to putting it out into the workplace. And again, that's so unless it has some ventilation system or lighting system attached to it does not offer that safety mechanism. So, the employer would be responsible to add that as soon as they bought the machine. Peter Koch: Sure, that's a great point. So, with you have a particular tool, don't rely on the manufacturer to provide everything because like you said, the OSHA standard says the manufacturer is not responsible. The employer is. Do your own assessment, go back to the OSHA standards. Look at subpart H, I or O depending on the industry. Check out the E tools and then I mean you can even reference I know that you specifically Hartley, have developed some resources for MEMIC that have helped our policyholders do machine guarding assessments and address some of the challenges that they have. So where might they find some of those things that MEMIC? Hartley Webb: I believe all of the forms that you're talking about are on our resource library within the safety director. So, if you go into our website, references safety director and then go to the resource library. We were actually involved in a NIOSH study. MEMIC was we have some great resources for assessing metal work machinery, but some of that does cross over. I mean, a bandsaw is a bandsaw, but it's a very, very detailed. And those go into the NIOSH requirements for machine guarding, which are much more extensive than what you would find in your OSHA regulations. Peter Koch: Sure. But that could give you a good resource, especially when you might have a more complex machine or you're really looking at something that kind of fits the OSHA standard but might not fit the OSHA standard. And you're looking for or you have a very dangerous operation and you want to make sure that you're protecting your employees, that the NIOSH places is certainly a place to go. And yeah, you're right, we we did participate in that study and there are a lot of good resources out there. So safety director is a good place to stop into. Hartley Webb: Those resources that we have available for them for the metal working. Like I said, they're detailed, but that's not only looking at fishing guarding, that's also looking at electrical, looking at lighting, looking at personal protective equipment, employee placement. It does a full hazard assessment of the machine, not just the guarding portion. Does they all time to work together with the clothing that the employees wearing, debris protection, access to hazard point. So, there's a there's a lot more being assessed than just the physical hazards and the requirements regarding. Peter Koch: Yeah, awesome resource for a general hazard assessment for machines, especially those metalworking machines. Well, thanks a lot for sharing all this with us. But we're about at the end of our MEMIC Safety Experts podcast. And I really appreciate that you've shared all this expertise with us. Hartley, but before we close, I've got one final question for you, because this is a safety podcast. Why is safety important to you? Why is it important to you, Hartley? Hartley Webb: Nobody out. It wants to get hurt or should be getting hurt. And it's easy. I've made it a point in my life to enjoy what I do, be a consultant and try to do the best I can to try to prevent people out there from being injured in the workplace. And it's in their best interest. It's a passion of mine. It's just something that I don't think is ever going to be a driving force. I'm gonna to, you know, give up anytime soon and, um, you know, I just I look forward to it every day. But it it's all about, you know, employees being able to go home to spend time with their families and, you know, enjoy their lives without being at risk while they're in the workplace. Peter Koch: That's awesome. That moral component of safety is a is a huge part. I can see it working. Having worked with you for the last 12, 19, almost 19 years now for me, that I can definitely see it in the way you apply yourself to the work that you do. So fantastic. I appreciate that, Harley. Thanks a lot. Peter Koch: So, again, thanks for joining us today. Thanks for joining us today. And to all of our listeners out there. We've been talking with Hartley Webb, safety management consultant with MEMIC, about machine guarding on the MEMIC Safety Experts podcast. If you have any questions for Hartley or like to hear more about our particular topic on our podcast. Email us at [email protected]. Also, check out our show notes that MEMIC.com/podcast where you can find links to resources for a deeper dive into this topic. Check out our website, MEMIC.com/podcast where you can find the podcast archive and find all of the ones that we've recorded prior to today. While you're there, sign up for our safety net blog so you never miss out on any articles or safety related news updates. And if you haven't done so already, I'd really appreciate it if you took a minute to review us on Stitcher i-Tunes or whichever's podcast service you find us on. And if you've already done that, I thank you very much because it helps us out a lot to spread the word. Please consider sharing the show with a business associate friend or family member who you think will get something out of it. And as always, thank you for the continued support. And until next time, this is Peter Kotch reminding you that listening to the MEMIC Safety Experts podcast is good but using what you learned is even better. People, Ideas and Articles referenced in the Podcast MEMIC – https://www.memic.com/ Peter Koch – https://www.memic.com/workplace-safety/safety-consultants/peter-koch Hartley Webb – https://www.memic.com/workplace-safety/safety-consultants/hartley-webb OSHA – https://www.osha.gov/ ANSI – https://www.ansi.org/ OSHA E Tools – https://www.osha.gov/dts/osta/oshasoft/ NIOSH – https://www.cdc.gov/niosh/index.htm