Hand Safety w/ Joey Geng
MEMIC Safety Experts - Ein Podcast von Peter Koch - Montags
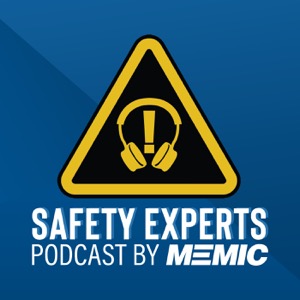
Kategorien:
The Bureau of Labor and Statistics reports in 2018 the goods and service producing industries had a hand injury incidence rate of 30.8 per ten thousand full time workers. And these are only the injuries that got reported. Think of all the times when you hit finger, got a paper cut, a splinter, or another small injury to you hand. That time, it might have hurt for a moment, but there is always the chance it could have been worse. The human hand is one of the most delicate and dexterous instruments we have to interact with the world. With them we can feel the heartbeat of another person, create art and music, pick a flower, or grasp a tool, adjust a machine, and pick up stock. Without them or without full use of them, we lose a big part of our sense of touch and how we interact with everyday things. According to the stats, it’s at the workplace where our hands are most at risk. If they are such an important part of our lives, why don’t we treat them with more care. In this episode, Pete explores what makes safety work using someone’s hands as the focus with Joe Geng, Vice President of Superior Glove and author of the book, “Rethinking Hand Safety: Myths, Truths, and Proven Practices”. It’s not a book that you would expect, it really is about how to rethink safety from the perspective of your hands, the pitfalls you will see on the way, and examples of how to move forward. Check it out on your favorite podcast platform or at www.memic.com/podcast. Peter Koch: Hello listeners and welcome to the MEMIC Safety Experts podcast, I'm your host, Peter Koch. Today, we're recording from the studios of Portland Pod. They have a full service podcast, recording and production studio right here in South Portland, Maine, and if you like this podcast and the way it sounds. Go ahead and get a hold of Tanner at PortlandPod.com. Today, we're taking an interesting look at hand safety through the eyes of Joe Geng, author of Rethinking Hand Safety and vice president of Superior Glove. Joe grew up among the tanneries of Canada, helping his father make gloves, and he has spent his entire life studying industry hand safety, doing glove R&D and consulting with leading companies like Toyota, Honda, Space-X, General Motors, Bombardier Aircraft and Shell Oil. The Geng family business Superior Glove is considered one of the world's most innovative glove manufacturers. Joe, welcome to the podcast today. Joe Geng: My pleasure, Peter. Peter Koch: Yeah. So it's really great to [00:01:00] have you here on the line. So I just want to kind of give you a little background here. When you first approached us to come onto the Safety Experts podcast, I thought, I'm not really sure about this we're really not about endorsing a particular safety product or service. And while it's important to innovate, at MEMIC, we believe that safety is not really about the newest tech or better piece of PPE. Then I read your book, Joe. And for our listeners, you might figure that a book on hand safety written by a glove guy would be just chock full of gruesome stories of mangled digits, missing limbs, stacks of regulations and requirements and endorsements to use a particular type of glove. Well, while they're stories, they focus the reader on the event chain. And while there are endorsements to use gloves, it's more about how and why to pick the proper one. There aren't any regulations in the book, and it's all about an exploration of what makes safety work using someone's hands as the focus. But what you describe [00:02:00] in the book can be applied everywhere, not just in your hands, but all over the place. It's not just a book that you would expect. It's really about how to rethink safety, using your hands and the pitfalls that we might see on the way and examples of how to move ahead. So, Joe, tell me about growing up in the glove industry and what inspired you to write this book? Joe Geng: Sure so, yeah. I grew up in the business. My dad bought the business in 1961. And my brothers both worked in it. And then growing up kind of through high school and earlier on, I worked part time in the business and more or less every lunchtime and dinner conversation was shrouded by gloves. So I was kind of in your blood in a way that just by osmosis, I learned a lot whether I wanted to or not. And this whole community, it's kind of interesting. We're just in a small town outside of Toronto, and the town to its core is a glove and leather town. I remember being at a, just a funeral [00:03:00] for some older gentleman. And then outside there was a bunch of older guys talking. And you think like in most small towns, they'd be talking about how their high school was their football record or something like that. And these guys were talking about how many gloves they would make after school and how much money they would make in the different club shops growing up. You know, and there's just kind of it's really part of the town’s culture. So it's an interesting place to grow up. It's just a lot of history and glove history for a couple of hundred years kind of thing. So then what inspired us to write the book is we just deal with a lot of customers and factories and construction companies and even when we recommend the right gloves, we found that sometimes they're still struggling with hand injuries and we really didn't know what else to do other than recommend that they buy more gloves or more expensive gloves or something like that. So we thought we got to take a step back and look at what are the other things we can do to try to help those customers. And then writing a book we thought would be an interesting way to just create the discipline that we would have to go through. And if we're going to write a book about it, we have to learn about it. And so that we thought was a good process to go about getting a better understanding of how to help those customers. Peter Koch: Well, it certainly shows reading through the book. You know, like I said initially, I was a little. Well, I didn't know what to expect, honestly. I've read a number of books on safety and some of it can be very regulation based and some it can be very specifically based on like behavioral based safety or metrics or something else. And you really did a really good job, I think, of journeying you or the reader through safety overall and really through the focus of your hands, which is your expertise. Like you said, it's in your blood. So it's a really interesting way to look at safety overall, but look at it specifically from the point of somebodies hands. And you made a point in the book right at the beginning to talk about sort of how you marvel at the hand itself and then what we take for granted. So in a past [00:05:00] life, we were talking just before about skiing. In a past life, I was as a full time paid ski patroller and we saw numerous injuries in some of the most challenging weren't always the worst. They were the hand injuries, the shoulder injuries. And I remember reading the book, what came to mind was a particular person, a grown man who we had just sent over to the clinic. He had an x ray and it had his hand set and casted after multiple digit fractures from a fall. And we were sitting and talking finishing up paperwork. And I just watched his face, go white and I'm like he's going to pass out. He must be in a lot of pain. We started talking to him and what his realization was. He wasn't going to be able to play piano at his daughter's wedding. And so just that piece about that fall, the injury on his hand, it changed a portion of his life that he was really looking forward to. So hands are a big deal. Hand safety is a big deal. And I [00:06:00] think you did a good, really good job at getting us to understand safety through that through focus. So tell me a little bit about the book. First, describe it first. If you had to describe this book to a safety manager and you describe three different types of companies and we could talk a little bit about that later. But in that third type of company, a company where that safety manager is working, he wants to get better at safety. And you think this would be a good book for him to read? How would you describe that book to him, how would you describe this book to him? Joe Geng: Well, I think the short version of that would be just it's kind of a summary of the best practices that companies use to reduce hand injury. So we went in there, really, we had a blank slate. We didn't know anything about safety, we knew gloves, but that's about it. So we went in and just researched. We did a lot of academic research. And it was really surprising how much academic research there is about hand injury reduction. And then we interviewed dozens of safety managers that we've seen at companies that have reduced their hand injuries. [00:07:00] And then we talked to safety experts that work with those companies. And then the final piece is we just talked to our sales team because we have a field sales team that are around these customers all the time. And they had a lot of interesting and colorful stories that add a lot to it. And so when you kind of put that all together, it was okay, this is what we know or what we've uncovered as some of the best practices for reducing hand injuries. Peter Koch: Right on. So you said you did a lot of research for the book. What sort of things did you learn as you went through the research and what was maybe surprising to you as you did that research? Joe Geng: Yeah, there was a lot of surprising things. Some of them are odd and some are funny. I remember there was one academic study that that dug into the factors that led to the likelihood of hand injury in the construction industry and so they've done this really thorough study and there was all kinds of interesting factors that you would not have thought of. So they said, for example, being a smoker puts you had an increase odd of a hand injury and I’m [00:08:00] not really exactly sure why that is. Maybe if you're smoking on the job, you're not paying attention or something. Not having played sports as a youngster made you more likely to get injured overall. Oversleeping, under-sleeping and oversleeping were both factors that led to higher rates of injury, which I would not have anticipated that sleeping more. It was more than nine hours a night made you more likely to be get a hand injury and then time of day. So there was a higher frequencies at certain times of day. So it was like mid-morning on Monday I think was one of the most likely times to get injured. And then also kind of the things that you would, I guess, think that maybe like Friday before a long weekend, there was higher injury rates, things like that. So there's really when there was attention lapses. So that was just one study, right? There was a whole lot of interesting things uncovered from that, just that one study. But overall, yeah, there was interesting practices around behavior based safety. That were found to be very effective. And I mean, I can I can talk for a long time about all the interesting and weird stuff. [00:09:00] And another one that really stood out that was kind of funny in a sense was there was an oil drilling company in western Canada. And they rolled out a campaign where they gave all the drillers, they gave them a pair of pink gloves. And they trained them on hand safety and said, if you see one of your co-workers doing something unsafe for their hands, we want you to go up and give them the pair of pink gloves. And they have to wear that for the rest of the day. And then for every incident or a pair pink gloves that you guys give out, they'll donate $5 to breast cancer research. And that campaign was a lot of fun. They had a good time with it. And there was it was taken, you know, in the right spirit of reducing injuries. And they saw a huge reduction in hand injuries and it maintained their hand injuries. I mean, stayed low even after the campaign was over. So that was kind of one of those interesting studies where they're engaging in effective peer pressure to reduce injuries. Peter Koch: Yeah. Right. And you had talked about gamification within your book as well. And that's one of those examples of trying to make safety almost competitive where because it comes [00:10:00] down to people together have the responsibility for each other's safety. So you've got to be paying attention. And if you know someone's watching, you're going to pay more attention. And that was, I thought that was really neat idea. And then tying it into the breast cancer donation really makes it almost fun. So it's not like I'm trying to get you. I'm watching. And if I do see it a I'm not just giving it to you because I want to show that you're doing something wrong. But the companies behind us in such a way that they're even going to donate money to a great cause. So fantastic way for that great example. Joe Geng: Yeah. The more that a company is able to make everybody the safety manager as opposed to just having one person with that title and do it in a good spirited way, then that really multiplies the effect of the safety program. Peter Koch: Yeah. Let's riff on that theme for just a minute so everyone being the safety manager, let's flip it around. Early on in the book, you talked about this concept of fatalism and how fatalism is immoral both at the management level [00:11:00] and at the worker level. So let's start there and talk about that for a little bit as kind of the start of the barrier to having the safety culture of everyone being the safety manager. So tell me a little bit about the concept of fatalism. Joe Geng: Yeah. So the most interesting story that illustrates that point that we came across, it was really powerful story. It was from Alcoa, the steel manufacturer. And it was when they had a new CEO that came in, Paul O'Neill. And pretty early on in his tenure, there was a fatality. So a young guy, I think he was like 20 years old. He'd hopped over this barrier to unclog this production line and he unclogged it successfully. Then a boom came around and killed him instantly. And then so Paul O'Neill brought all his plant managers and safety managers in. And he said they were all grieving for the loss of this kid. But at the same time, it was like, well, that's really unfortunate. It's an unfortunate part of the workplace that it's dangerous. And Paul O'Neill took a step back and he said, no, that's not the right answer. The [00:12:00] right answer is everybody in this room killed this kid. You killed him. I killed him. We're responsible for his death. And they said, whoa, whoa, whoa, whoa. That's going too far. It's not our fault that he did something stupid. And Paul O'Neill said, actually, yes, it is your fault and my fault that we didn't train him well enough. There's all kinds of steps we could have taken. And basically that it was our fault and that we can't take the attitude that. This is just a part of the workplace that needs to be fixed. So he had a hill to climb there, but he did change that culture from one that accepted injuries as a part a part of everyday life in an industrial setting to one where he said, no, we're going for zero. And then when he said that they were like, you are crazy, that's not possible. It's going to be financially too expensive to do that. And he just wouldn't take that as an answer. He said we're going for zero injuries. Peter Koch: Yeah. That kind of leads into that safety attitude of the entire [00:13:00] company starting right at the top. Like if Paul hadn't said that as the CEO at Alcoa. I think someone would have said that, yeah, we're responsible. But if the top dog doesn't get behind it and doesn't realize that he has just as much responsibility for the injuries, whether it's a splinter or a fatality, he has just as much responsibility for those injuries as the supervisor, the manager, the director, the foreman or the brand new person who comes on. You'll never make a change. And that that's a great I mean, it's a truly unfortunate example that it has to happen sometimes. It has to happen that way for a company to realize how challenging the problem is. But in that case, he was able to turn it around. He had great success at Alcoa during his time there. So he was able to, as you said, climb that hill and really get beyond the fatalism [00:14:00] piece and making safety something that is culturally accepted, not just culturally acceptable, but something that everybody just does not something extra. Joe Geng: And kind of further to your point on fatalism. A lot of times when you look at an accident that is seemingly random, but if you if you actually kind of brainstorm like what are the things we could have done to prevent this injury? And there's actually a lot that you really can do to minimize those options or the risk of that happening again, whether it's training or guards in place or when you sit down with a team and brainstorm, you can really come up with some interesting ideas and then there's a lot more that's under your control than maybe you would have thought otherwise. Peter Koch: Yeah. And having actually having sat through those both in business prior to my working for Maine Employer's Mutual Insurance and now working for MEMIC sat through those meetings, they can be incredibly productive. When you sit and brainstorm what are all the potential [00:15:00] conclusions or causes that you find when you're going through a post-accident or post-incident analysis. But you've got to stick through them because the first time that you do it. Can you just imagine the conversations that happened after the next injury that happened at Alcoa after that? So they've just went through. Everybody's responsible. You're all responsible. Everybody's responsible. So now you sit down and of course, with responsibility comes accountability. And everybody's thinking, well, if I'm responsible am I going to get fired if I talk about this? So you really have to work through those cultural challenges of the barrier for people, to be honest with you, with those conversations, especially the post-accident conversations. But the fruit that it bears, if you can do that, is amazing. But you've got to stick with it totally you have to stick with it. Joe Geng: Yeah. Yeah those kind of accidents and then also the like, the near misreporting that is really challenging for a lot of companies to get, to encourage honesty [00:16:00] in those situations. It can be really tough. What we see is a lot of companies that just kind of go through the motions, checking the boxes, but they're really not getting at the core and trying to find what those real issues are. They're kind of afraid of uncovering those problems. Peter Koch: Yeah totally. So let's give a hand safety example where there's been a hand injury and it can be something small or can be something major that maybe you've seen or been involved with where you've actually helped the company sit down and go through that process to come to the conclusion of what caused the event to occur. Do you have any examples that you could share? Joe Geng: Yeah, ok one example from the book and those kind of a startling example is one of our sales guys in Quebec. He went into pulp and paper mill and they just recently had a bad accident where a guy was holding a doctor Blade. So these heavy blades that they used for cutting rolls of paper and slipped and then cut [00:17:00] his belly and the safety manager product sales guy, and he said, OK, you're going to need these highly cut resistant gloves or you need to cut resistant aprons. We're going to cut resistant pants all this sort of stuff. And the sales manager just took a step back and said. Or the sales guy said, why is this guy walking around the plant with a blade in his hands? Why don't you just build a cart out of plywood or box out of plywood? Put the blade in there, put it on a cart and you eliminate that hazard altogether. And that's something the safety manager should have known and taken that step back. But it took somebody from the outside looking at the problem and thinking about it a little bit of a different way. So That's the kind of thing where ok you're jumping to a solution. But maybe you need to kind of uncover what are the other possible solutions to that issue that are much more effective and much less costly. Peter Koch: Yeah, that's a great actually lead in to talking a little bit about the hierarchy of controls, which you discussed [00:18:00] in your book there fairly extensively. So I'm going to just I'm going to describe it for a second. But you had two amendments to that, which I think are pretty important. So, of course, there is elimination at the Top and the suggestion of personal protective equipment that the supervisor gave in that particular or the safety manager gave in that case that you described, would have helped a little, but would might not have prevented the event from occurring again. So the cart eliminates the need to carry. So that's the best solution. And then you've got substitution, engineering, administrative controls. And then finally, at the end of this is personal protective equipment. And I thought it was really interesting that your sales guy. Right. So that the glove guy who's going in to sell more personal protective equipment provides the solution of elimination. So and a much better solution overall. So you provided two amendments to that hierarchy of controls. Can you describe what those two amendments are and how they fit into the safety [00:19:00] culture philosophy you have? Joe Geng: So I think when a company is trying to reduce injuries like hand injuries specifically or injuries overall like that, the first thing you want to do is that hierarchy of safety controls. That's the most effective thing for sure. And but it shouldn't stop there. And so there's lots of other things that can be done. So for example, behavior based safety, which in some safety circles has gotten a bad rep, but it's actually very effective when done properly is where you're looking at the behaviors that that people do. Recording this behaviors, reporting how often they happen and then working to eliminate them and where it's gotten a bad rap. So we've seen some stuff from some unions and things like that where companies are using behavior based safety instead of using the hierarchy of safety controls. And they call it blame the worker safety. But done properly and done with workers is actually a very effective way of reducing injury. So an example that I give just from one of the workplaces that we saw using this is they were doing a job where they had box cutters at a table and they were cutting some [00:20:00] product, they're kind of like trimming the product. And when they looked at where their injuries were coming from, a lot of the hand injuries coming from just somebody grabbing the knife or putting their hand on the table by accident and then getting cut on an open box cutter. And then so all they did was they created sheets for the box cutters to be put away. And then they had somebody in the workplace just one day a week. They would take 10 minutes and record how many box cutters were left open and then they put a chart up. And then they said, OK. This is how many we're seeing in a week, what can we do to eliminate that? And then every week they would have that person recording. OK. Now there's sort of ten this week, there's five this week and then the following week there's two. And they were really able to reduce those injuries. And then when you kind of multiply that across all the different injuries you're seeing, that's when you see some really good injury reduction. So in addition to that hierarchy of safety controls, behavior based safety is very effective as well as basically anything at your disposal that you can add to that. And the way we look at is like. Ok. It's like if you're getting in a car, you're not going to say, OK, I'm in a safe car and I'm driving on a good highway, [00:21:00] I don't have to buckle up my seat belt. You're going to buckle your seatbelt. You can do everything that you can to try to be safe. So anything you can add to that mix that helps reduce those injuries. Definitely use that. And then the no broken windows. That was from a New York City Police is where they took the attitude to try to clean up the city and to not look past the little crimes. And then they found that when they did that, the major crimes like murder were dramatically reduced. So it's kind of this odd thing, like we're going to stop the jaywalker and then in the end, that's going to result in a reduction of murders or serious crimes. But it was very effective. So this same kind of principle applies a workplace if you overlook the little things and then those bigger accidents tend to happen. So it's kind of paying attention to the small details and having a tidy workplace in addition to that. Housekeeping can be surprisingly effective injury reduction as well. Peter Koch: Oh, totally. I completely agree with that. I go [00:22:00] back to my grandfather when he was alive and he was a school teacher and he was a woodworker. And in the basement was his shop. And when I was younger, he died when I was eight. So when I was very young, I would go down into the basement. And when he wasn't there, well, when he was there, I would watch him work and he would make furniture and tables and things for my grandmother. But when he wasn't there, I would go take tools off his bench in the workshop and I would play with them. And of course, then I'd get distracted and I wouldn't put it away. Well, of course, when he walked down to the shop, he knew because every tool had a place. Once I figured out that he could look at the workbench and know if anything was missing because every tool had its place. I realize that if I took it off, I had to put it back because there was a gap. There was a hole. Something was missing so that no broken windows is a I think a really great thought process to help you to ensure that safe [00:23:00] culture throughout the workplace. So watch pay attention, have a process, make sure that the little things are taken care of. And I almost think that goes to your description of right at the beginning of the book, which really caught my attention of the three different types of companies that you'll walk into or work with. Can you describe those three companies and kind of how that no broken windows kind of fits into this description of those three companies? Joe Geng: Sure. Yeah. So the first kind of company is those companies that have a great safety culture. And you just know when you walk into a place like that, it's typically brightly lit, the floor is clean. And just like you said, every tool has a place and you just get a sense of order when you walk in. And it reflects on the people's attitudes. You know, that people are engaging, they're not suspicious, that sort of thing, because they know that management has their best interests at heart. And so you just walk in and you kind of know right away what the safety culture is without even having to do very much investigation. Then [00:24:00] the third kind of company is those companies where it's more or less the opposite. So things are dimly lit. It's grimy. And I mean, that's relative, right? Like some industries are just like you're not going to go to an oil company that's going to be spotless or something. But you get a sense of that there's order. So those places there's that lack of order things are lying about unnecessarily. And then typically they're using the wrong personal protective equipment as well, they're using the cheapest thing that they could get away with. Peter Koch: Or none, right? Yeah. Joe Geng: Or often none. Yeah. Or it's not worn or something like that. And then there's those companies that are kind of in the middle that they're struggling between the two. They're trying to get to be the first. But maybe they have a history of some of the behaviors of the third type. And so it's sort of a spectrum, I guess. Peter Koch: That concept of no broken windows, you look at that best type of company and there are no broken windows, or if there is a broken window, it's identified and it's corrected. Right off the bat. Peter Koch: Let's hit pause for a moment. To take a quick break to [00:25:00] consider how hand safety can be an indicator of your workplace safety culture. Look around your workplace or if you're not there, think about it. What are the jobs that put hands in danger? What's the condition of the gloves that the workers are wearing or are they wearing any at all? If you needed to get a pair of gloves from a supervisor, would you be supported or questioned for needing them? Do you see some indicators that there could be some gaps in your safety process? Well, in this podcast, Joe shares some interesting ways to see hands in your safety culture. Do you need some help figuring out how to move your safety culture ahead? Or maybe you got that wired, but you're looking for some different ways to assess your workplace for PPE. So check out the resources at MEMIC.com under the workplace safety tab where you can find free written resources. Our safety net blog and our podcast archive. And if you're a policyholder with MEMIC, you can log into the MEMIC safety director to dig deeper into the online resources that MEMIC has [00:26:00] to offer. Now let's get back to today's conversation. Peter Koch: On the opposite side of the spectrum. There's broken windows everywhere. So there are things that could be fixed, but it becomes normative for the people working there. And they don't expect the change. They don't think there should be a change. They've tried to change, but they're not getting anywhere. So they've just they're at the fatalism place where injuries are going to happen. It's a dangerous job. We're not going to fix it. Let's just keep going until we can't anymore. And then that middle company where there's you're going to have broken windows, they identified that and they're trying to keep up with it and they're doing the best they can to manage it. But they might not have all of the answers or all the tools that they need. Like they might not know how to choose the right glove or the right PPE or eliminate the hazard because they just don't have the experience or they haven't [00:27:00] engaged the employee into that. Joe Geng: Yeah, exactly. Yeah. To kind of reinforce that point. There was a study done at a shipyard and they engaged in this basically just to have a very thorough housekeeping process where every tool had a place. Previous to this, it was disorder and chaos. And then they did this where they tidied everything up, every tool had a place and created a much more orderly environment. And the safety manager was involved in that. They just estimated maybe a 10 percent reduction in injury because they attributed 10 percent of the injuries to like tripping on stuff and that kind of thing. But instead, they saw a 70 percent reduction in injury. So it was like a really effective safety program. Just by tidying up. Peter Koch: Wow. Well, it's just from the housekeeping. Really focus on housekeeping. Everything has its place that they were able to realize a 70 percent reduction in injuries. Joe Geng: Yeah, exactly. So can you imagine if you're applying, you know, effectively applying the hierarchy of safety controls, working on your safety culture, and then you [00:28:00] add a housekeeping program, you know, like you're kind of put all those things together and then you're going to see some pretty good results. Peter Koch: Right. Yeah. And that talks about the sort of how when you start a program and you gain people's respect about the particular process that you're going to use. And they can engage in the program that it really will go beyond just housekeeping, because I would imagine that, yeah, if I'm going to not trip on stuff, we're going to have a 10 percent reduction. But in order to deal with all of the hand injuries and the injuries that are caused by not paying attention and the injuries that are caused by having to go walk 30, 40, 60 paces to go get something and then come back. Those causalities will be captured in the housekeeping piece because it's just going to it's going to translate from one place to another. Joe Geng :Exactly. Yeah, surprisingly effective. Peter Koch: Yeah. You also talked a little bit about this concept of what's normal and [00:29:00] trying to look at your business, your company as like you're going to look at it and you're going to understand that this is normal. But sometimes it takes a fresh set of eyes or the safety manager to look at it with a fresh set of eyes to understand that things aren't normal. Can you talk a little bit about that? Joe Geng: Sure. Yeah. So kind of goes back to that, the earlier point of fatality that or fatalism where you're thinking oh this is inevitable, but with a fresh set of eyes like what we've seen in a lot of companies, that they've dramatically reduced their hand injuries or basically eliminated them. So that's kind of the point we're trying to get across, is that you're having hand injuries. You don't have to accept that as an everyday reality, that with the right programs and tools in place, you can. You can go for zero injuries kind of thing. And so the challenge sometimes from the safety manager, is that if you have employees that have been there for a long time, they accept that, oh, I'm just going to get injured or the cuts and that kind of thing [00:30:00] that's part of working here, that to kind of overcome that, it can be challenging and then it can be also challenging if you have a lot of employees that are born in other countries. So if they're from Latin America or really anywhere else that doesn't have a great safety culture, that they will be more prone to engage in behaviors that are dangerous and then not bring up those things that said maybe somebody born in Canada or the US would consider as dangerous. When we talked to one safety manager at a construction company and had some workers that were from Syria and he had a tough time getting the wear PPE and do other things safely and they more or less told him. We're used to being, we're coming from a wartime environment and this construction spot is the safest place I've ever set foot in. So I think it's no big deal that I'm not wearing my hardhat. I'm used to being shot at. So like you have that extra step to overcome, right. That their attitude was all right. I'm fine. Everything's going to be OK. Peter Koch: Right. And if he hadn't had that conversation with those workers, he might never have understood what the reason is. I mean, he probably told [00:31:00] them 100 times to put your hard hat on, but they keep forgetting because it's just not part of their culture. It's not they don't see it as a hazard or a danger. It's not like their normal is very different than his normal. Joe Geng: Yeah. And even more like their outlook on the world was that from certain cultures was that this is in God's hand. So I don't really need to act safely because what will happen has already been predetermined by God where you're like Americans more than anybody. Let's take ownership from outcomes in my life and that kind of thing. But not everybody's grown up that way. So they really have to take a step back and look at our assumptions, right? Peter Koch: Yeah, absolutely. And there's a phrase that you had in the book that I think sums it up pretty well. As a manager, you have a vital responsibility to get as far inside a worker's head as you can. And I think that story that you brought up highlights that really well, you've got to know where your employees are coming from. You got to know what their backgrounds are, at least in general. You might not need to know exactly [00:32:00] what they do when they leave the construction site. But to get an idea of what their normal is can really help you not just encourage, but teach and train them so that they can see a new normal. Joe Geng: Yeah. Yeah. I mean, that's easier said than done too, right? Especially if you're meeting somebody from another culture that maybe their English is not perfect and then they might not be that open with their boss. That kind of thing. So as much as you can do it, that's great. But it's not always so easy. Peter Koch: Yeah. And then you get some pushback certainly from managers and supervisors and safety managers like, oh no, I got this. These are all my people. I get it. No problem. You know, I used to do this a long time ago. These are my people. And really if you don't step back and take stock of what's really happening and look at the workplace and the activities and the behaviors with a fresh set of eyes, you're going to miss something. And when you miss something, you're really putting your workers at risk. Go [00:33:00] back to that example of in the paper mill where they just had an injury where a guy carrying a really heavy and a very sharp blade by hand from point A to point B cut himself. And then the solution is, well, we're going to have more PPE. Well, if we can look at it with a fresh set of eyes, we can look at it from a very different perspective. And sometimes that's getting the workers involved. Right. So I can't just do it by myself. I actually have to get the workers involved in it. Joe Geng: Yeah, we spoke to a guy at the University of Colorado, Matthew Hollowell, and they've done an interesting study where they had safety managers kind of walk through workplace and safety managers who are trained only identified about forty five percent of hazards. So you mean they're missing 60 or so? Fifty five percent of hazards and missing more than half. And that's just are human nature, right? That if we walk through, we quickly see what we think is hazardous. But we really miss a lot. And so it's a challenge. How do you go from that forty five to trying to get to ninety [00:34:00] five or hundred percent? It's kind of bringing in that fresh set of eyes or a couple different sets of eyes, you know, not only for your own safety manager, but somebody on other workers or maybe somebody that's not in that environment at all, you know, or an outside safety consultant. The more you can do that and more of those hazards you're going to identify because they're just with our eyes. We're just going to we are really going to miss so much and overlook some of those things. Peter Koch: Sure. Because we definitely come into this with some biases. Right. We're going to have cultural biases, will have different biases that will see the world through which we might end up turning a blind eye on to something. We might not recognize it as a hazard. So, yeah, a fresh set of eyes. And you do talk quite a bit about biases in the book. You have a whole section on that. Can you describe a little bit how bias can either help or hinder us as we assess the environment for hazards? Joe Geng: Yeah, there's all kinds of biases that that affect our ability to objectively judge really anything. [00:35:00] So workplace or any other thing. So one example was there was a mine that had caved in on some workers and then they went back and looked at the like the pre-work analysis. And they said they had inspected the mine shaft and they said, everything's in order. Everything's in place. Everything's perfect. And then when they actually looked at it, I think it was like one hundred and twenty bolts were missing from this one structure. And so really, it was in bad shape, but they had checked it off as all the bolts are in place. So just in that case, you kind of have confirmation bias, you're going in with it assuming that everything's fine and then checking the boxes quite quickly then. To give you an example, if you have two drills or two like augers drilling into the ground and one is moving from our human nature, we'll judge the moving auger as dangerous. But then the reality if the other auger is stuck and not moving. That's the one that's building up energy and is about to blow up. And so there's like this potential energy that just from the way our human mind is structured is we see something that's not moving, we consider it [00:36:00] safe, when really that could be the thing that's much more dangerous. So we have a bias when we're doing hazard assessments to see some things as dangerous and other things as not. So like that kind of potential energy that's being built up like an electrical box that could blow up and kill you. It could be turned off and be totally safe. Or it could be about to let out an arc flash. But those are the kind of hazards that we don't typically identify because it doesn't from our mind. It doesn't look dangerous. Peter Koch: Yeah. That's the reason why people put their hand in a snowblower. Right. Because it's the impeller get stuck because it's plugged up with snow. Nothing's moving. I'll be fine until they lose a finger doing it. Yeah, I totally get it. Yeah. Joe Geng: Yeah. Embarrassing stories. I did that exact thing with a blender. So I was blending up food for my son who was quite young at the time. And I without thinking, just like there was a total lapse of thought. I put my finger into to unclog this blender and then cut my finger quite badly and had to go get stitches and [00:37:00] then come to work. And I can imagine the hard time you're given as a cut resistant glove expert who has a stitches. Peter Koch: Yeah. Oh, my goodness. Joe Geng: Yeah. But it's a couple of lapses in attention. Peter Koch: Yeah. Absolutely. So there's so much in this book that we can talk about, and I really would like you to come back at some point in time and we can go into depth and some more of these subjects. But I do have one more question for part of the book, and it comes from the section that's titled For the Want of a Proper Glove. And you have a description of a proper glove, and I'm going to quote it here, "the proper glove is the one that meets the minimum requirements and that people will actually wear." So and you then you go through and you describe what that statement actually means. So can you take me through what that definition means? And maybe we can actually look at that not just as it applies to gloves, but as it applies to safety over [00:38:00] all. Joe Geng: Sure. So what we see, a lot of safety managers making this mistake is that when they're specking a glove, they will over spec. So if they need a certain level of protection, they might go two or three levels higher than that just to make sure that no injuries happen. But what the downside of doing that is you're getting something that's less comfortable. So we advocate for really. I mean, you have to have something that's actually going to protect your hands. You don't want to wear nothing. But as long as you're meeting those protection requirements, that comfort really has to be a huge factor in glove selection, because comfort is what's going to mean somebody's wearing the glove or not wearing gloves. And where there are there are studies done by Liberty Mutual where they show that 70 percent of hand injuries are the result of people not wearing gloves in the workplace. So it's like the gloves are too cumbersome. They're taking them off to do some fine motor tasks. Then likely forgetting to put them back on, and then they're getting a hand injury. That's what we see a lot in the workplace. So that's where we really advocate for really choose comfort, get workers involved [00:39:00] in the selection to make sure that they can actually do the job wearing those gloves. So given the choice of over protection or erring on the side of comfort, we'd advocate for erring on the side of comfort. It's going to be compliance because the best glove is one that someone actually wears and not one that's going to sit in the tool chest or chest or somebodies back pocket. Peter Koch: Yeah, that's a great thought process. So like it meets the minimum requirements. So if it's got to be cut resistant, it has to be able to resist, at least at a minimum, what the worker is going to be handling and that it's got to be it's got to fit well enough, be made of the right material and comfortable enough so that the people will be able to wear it to do the rest of their task. You had a couple of descriptions in there where, you know, you had a company that was working with metal all the time, but they had a touch screen that they had to use after they handled the metal. So what would happen they'd handled the metal? They take their gloves off to touch the touch screen and then they may or may not put the gloves back on to handle the metal. So [00:40:00] in the book you described that your company was actually able to come up with a solution so that they could have touch capacity through the glove with the fingers so that they could they didn't have to take the gloves off anymore. So, again, minimal requirement. So there's numerous examples in the book that you go through that talk about the wrong piece of PPE, or the wrong glove versus what makes the right glove for this particular situation. Joe Geng: Yeah. And luckily, material science is getting a lot better. There's just some more materials coming out and better and better engineering in place. Gloves are getting more and more comfortable over time. So what people who are 20 years ago would be considered really bulky, to what they're wearing now and then hopefully five or 10 years from now, you'll be able to get those really high levels of protection and barely feel like you wearing a glove at all. Peter Koch: Yeah. And even now the difference between what I was wearing 20 or 30 years ago versus what I can wear now for cut resistance. The tactile sense that I have, the agility that I have with my hands because of the different [00:41:00] fabrics that are there is just amazing the difference. So if you are 20 years ago in technology, there's something new that can do the job and even better than the old glove could. So, you know, I always, always look forward, but understand what your hazards are and don't try to overthink it too much. Joe Geng: Yeah, that's sure. Yeah. The gloves are one of those interesting things where they're really personable. Right. So it's hard, sometimes hard for people to make a change because they like what they've been using for 10 years or something like that. But it's remarkable how emotional that decision can be sometimes. Peter Koch: It really is. That's a it's a it's a good point. We're coming right to the end of our time here. Joe, is there something that you would like to leave our listeners with before we close? Joe Geng: Yeah, I guess it's just that knowledge for the safety manager or that encouragement that if you stack up those small wins, it can really lead to big results so that a safety manager can sometimes get overwhelmed or discouraged that they're not having success. But if you can kind of stack up those wins, so even if it's picking a better glove or getting a better house keeping program in place, [00:42:00] if you can start headed in the right direction. And make those improvements. That over the long haul, that's going to have a huge impact on the safety culture of that company. Peter Koch: Yeah, definitely. Cause safety sometimes is that elephant in the room. And if you eat the elephant one bite at a time, it's not going to choke you. So that's a great piece to leave us with there, Joe. So that really wraps up this weeks Safety Experts Podcast. And thanks for sharing your expertise with us, Joe. Where can people find out more about you and about your book, Rethinking Hand Safety? Joe Geng: So we have a Web site for the book, RethinkingHandSafety.com Or just superiorglove.com as well. Peter Koch: If someone has a specific question for you, what's the best way to get a hold of you? Joe Geng: Probably Linked-In or my email address is Joe J-O-E at Superiorglove.com Peter Koch: Today, we've been speaking with Joe Gang, vice president of Superior Glove and author of the book Rethinking Hand Safety. If anyone would like to find more information about hand safety or like to hear more about a particular topic on [00:43:00] our podcast. Email me at [email protected]. Also check out our show notes at MEMIC.com/podcast Where you can find links and resources for a deeper dive into the hand safety topic. Check out our web site www.MEMIC.com/podcast where you can find our podcast archive. And while you're there, sign up for our safety net blog so you never miss any of our safety articles or news updates. And if you haven't done so already, I'd appreciate it if you took a minute or two to review us on Stitcher I-Tunes or whichever podcast service you find us on. And if you've already done that. Thank you. Because it really helps us spread the word. Please consider sharing the show with a business associate friend or family member who you think will get something out of it. And as always, thank you for the continued support. And until next time, this is Peter Koch reminding you that listening to the MEMIC's Safety Experts Podcast is good, but sharing what you learned is even better.