Packaging Validation Best Practices
Global Medical Device Podcast powered by Greenlight Guru - Ein Podcast von Greenlight Guru + Medical Device Entrepreneurs - Donnerstags
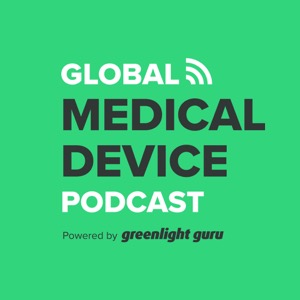
Kategorien:
The packaging of medical devices, especially sterilized products, is often overlooked and does not make news headlines until it’s done wrong. How can packaging and labeling prevent 510(k) delays? In this episode of the Global Medical Device Podcast, Etienne Nichols talks to Jeff Barrett, CEO of J-Pac Medical, about packaging validation best practices.Jeff has 25 years of experience in the medical device industry, specializes in getting new devices to market, and scaling your commercialization. He has extensive knowledge and understanding of ISO 11607-1 & -2, Packaging for Terminally Sterilized Medical Devices.Some of the highlights of this episode include:Sterilization validations/revalidations take a lot of money ($40,000-80,000) and a long time (16-20 weeks) to complete.Don’t underestimate labeling - 40% of FDA recalls are due to labeling. Make sure your CM has good labeling controls.Over a third of all package validations fail the lab test for transit. The biggest reason why companies fail packaging validation is not understanding the various shipping modes and their related testing.ISO’s 11607 standard has two parts: Part 1 is about designing the package; Part 2 is validating the package. Also, there is a guidance document due to the complexity of the packaging process.The criteria for filing a 510(k) and steps related to packaging include validating that the seals are good from a sterile barrier standpoint and the product is good and has not changed over time because of transit testing or aging.From a design standpoint, document how the package has been designed and meets customers’ needs. Recently, the FDA added user testing to the standard for sterile transfer.Feasibility testing of prototypes and samples of vibration, drops, and humidity should be conducted to prevent potential problems. Ask engineers about product changes and the risks for redesign of packaging to know if the package will fail or pass.Memorable quotes from Jeff Barrett:“The FDA looks at a standard called ISO 11607. That is the Bible for medical device packaging validation. There’s two parts to it, Part 1 and Part 2. Part 1 is all about designing the package and Part 2 is about validating the package.” “Over a third of all package validations failed at the lab for transit. It’s staggering.” “Less so do we see damage to the product itself. So, I’d say, 8 out of 10 times on these failures, it’s the product and the seal failing, not the product breaking.” “One of the biggest problems we see is, (the FDA) they don’t do any validation. They say, ‘We’re going to do it later.’ That’s obviously a problem. You can’t market the product if the package hasn’t been validated. That’s why the FDA gives you a break on that.”“The bottom line is you’re trying to maintain the product without getting damaged and without the sterile barriers getting damaged. That is the end goal.”Links:Jeff Barrett on LinkedInJ-Pac MedicalEtienne Nichols on LinkedInISO 11607-1ISO 11607-2ISO 13485ASTM International